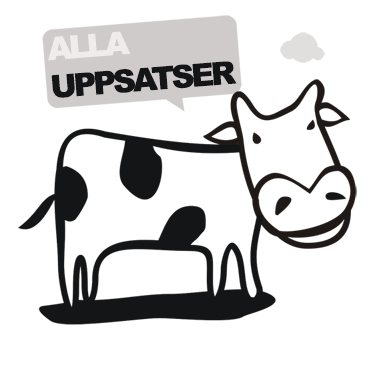
Reglering av turbins ledskenor i vattenkraftverkmed hjälp av elektriska ställdon
Hydropower is the largest renewable energy source available in today's society. Operation and production is handled by high-tech electronics. This thesis is done on behalf of Statkraft Sweden AB who wants to explore the possibility of replacing the hydraulic cylinder with an electric actuator, generally as well as a case of a small power station on the river Nissan. Whether it is the chaplain or francis turbine vanes are actuated by hydraulic cylinders. Because of Gustavsberg hydropower is inconstant operation, this report is based on power calculations, which are read and computed according to the available hydraulic diagram. With the system operating pressure of 100 bars determined that the hydraulic cylinder on Gustavsberg power stations is sized for a force of 143kN. Based on this force, it has committed to fit a suitable modular actuator from SKF.Electric motor is determined according to actuator screw parameters which are implemented in MATLAB to find out which torque is needed to power the actuator. Two options are suitable for the application. One is the complete drive packages from SKF with AC servo motor and controller to this, the other is asynchronous motor from the appropriate manufacturer such as ABB, together with drives from the same manufacturer.Since the actuator will not work more than twice an hour, there will be needed holding torque for the actuator to maintain its position. Holding torque is achieved easiest with an inverse function of the mechanical disc brake. This can be applied both during operation of the servo motor or asynchronous motor.Security is key in a hydroelectric power station thereof demands on the components involved in the closure of the turbine. In the current situation the power station is equipped with two independent systems to shut off the turbine at degraded situations as power failure or fire. The first system consists of the UPS device, the other is a counterweight at 2600 kg. This thesis makes the assumption that the UPS system has fallen away and the only thing that remains is the counterweight. The counterweight issued to turn the vanes if the hydraulic system loses pressure.In degraded situations problems occur with actuator when the actuator backwards runs due to the influence of guide rails and counterweights force. To solve this problem it has been developed three solutions suggested methods. Regenerative braking is most appropriate when the actuator is driven by servomotor. Industrial damper or modification of the actuator is possible to implement regardless of the operation of the servo motor or asynchronous motor.