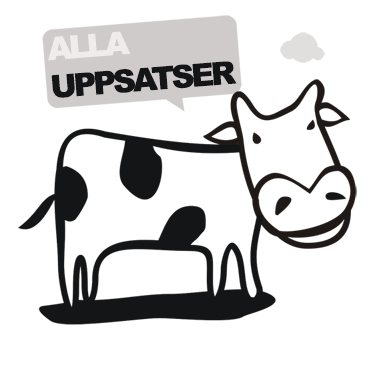
Hur kvalitetsstyrning kan förebygga avvikelser i en terminalprocess.
DeviationInformation flowQuality managementLeanService sectorAvvikelseInformationsflödeKvalitetsstyrningLeanTjänstesektor
In todays competitive business climate the concept of ?quality management? is a significant part of daily work for many companies, as they want to achieve high performance quality and delivery success. Within the services sector third-party logistics companies play an increasingly central role when it comes to the goods that are being transported. These companies are presented with continuous challenges to ensure that goods are loaded on trucks efficiently and delivered on time, at the right place and in the right condition. The present case study was conducted in collaboration with Schenker AB and Schenker Åkeri in Jönköping, to help these two company branches serving under the same major corporation to solve a common problem they both encounter, namely the fact that it regularly occurs handling abnormalities in the terminal process that affects overall quality for customers.The study aims to find out how the daily quality control concerning the handling of goods in the terminal process can be improved hopefully resulting in a higher quality in cargo shipments. The aim of the study was approached by trying to answer the following two questions:What are the causes of management deviations in the terminal process and how can these be grouped into different classes?How can quality control be changed to prevent these handling deviations?The approach has consisted of a parallel collection of data and theory in order to continuously relate data and theory to find a coherent context for the problems that these branches are facing. Primary data has been obtained through observations and interviews from both branches. Secondary data was collected through a survey conducted by Schenker Åkeri regarding information flow in the present situation and the desired position of drivers. The results of the inquiry have shown that most of the deviations in the terminal process occur when the operator performs a task incorrectly, also known as handling errors. Furthermore, the study has shown that the information given regarding certain operations has been inadequate and not sufficiently clear, thus this has shown to be one of the reasons that handling errors occur. As a result, the framework for all proposed meetings was prepared with guidelines regarding what the meeting should include for the respective departments, as well as important advice to remember while performing a lean meeting.To correct and avoid handling errors that occur on an operational level, it is recommended the information architecture be improved. Thus, this was elaborated in the form of regular meetings based on the Lean philosophy between labor management level and operational level. Deviations are prevented also by a standardized approach, and visualized and distinct markup for what may be placed at any location. A significant aspect of a company is to create commitment and motivation of all employees at all levels. Collaboration between the two company branches is important when working in close proximity, meaning that the actions of one branch of the company will affect the others, and vice verse. In conclusion, we recommend that the branches work together to create a common vision applied within both Schenker AB and Schenker Åkeri."Community and collaboration creates quality and customer value!"