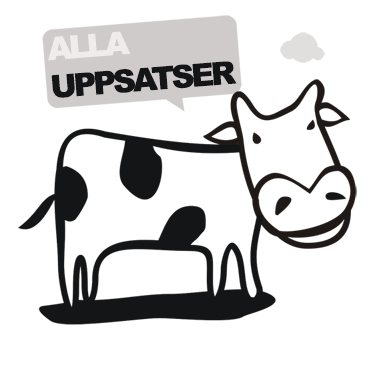
Utvärdering av en Magnetic Harmonic Traction Drive
In this report a new gear concept is evaluated using the magnetic finite element method (FEM)software MagNet and Ansys as well as the mechanical FEM software Abaqus. The gear conceptis evaluated in terms of maximum torque capability, torsional stiffness, gear ratio and efficiency.ABB Corporate Research has proposed a new gear concept which should be less expensive thangearboxes used today. The new concept is called aMagnetic Harmonic Traction Drive and usesthe principles of a harmonic drive gear to achieve a high reduction ratio. The gear conceptreplaces the wave generator used in traditional harmonic drives with magnets and uses tractioninstead of gear teeth to transfer the torque. The main components in the gearbox are the magnets,the flexspline, the magnetic portion and the circular spline. The goal of the gearbox is amaximum torque capability of 5 Nm, a torsional stiffness of 2000 Nm/rad, a gear ratio of 100, anefficiency of 50 % and a maximum diameter of 100 mm.A model of the gear concept is built in the magnetic FEM simulations software MagNet toevaluate the choice of magnets used in the gearbox as well as the dimensions of the magneticportion. The results from MagNet show that a magnitude of 120 N can be expected from themagnets used in the gear concept and the force distribution. The losses caused by hysteresis andeddy currents are calculated to be bigger then ideal ingoing effect, giving an efficiency lowerthen 50 %. The magnetic finite element software Ansys is used to validate the results fromMagNet, a comparison between the two programs shows some correspondence when comparingthe total force but poor correspondence when comparing the force distribution.The FEM software Abaqus is used to simulate the mechanical behaviour of the gear concept. Amodel is built up using the flexspline and the circular spline. The total force and the forcedistribution from the MagNet simulations are applied to the model to represent the magnets inthe gearbox. The model predicts a torque capability of 1.5 Nm for the gear concept, a torsionalstiffness of over 2000 Nm/rad and an expected gear ratio of around 80.The results from the simulations are used to give recommendations to the construction work ofthe gear concept. Recommendations are given for which type of magnets should be used, theirshape and size and of which material they should be made. Suggestions for appropriate materialsand dimensions for both the flexspline and the circular spline are given, as well asrecommendations of possible future work for the gearbox.