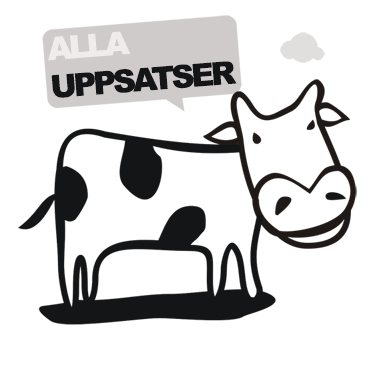
Smörjningsfri led till industrirobot
IRB 340, Flexpicker is an industrial robot used for sorting, packaging and the handling of details up to two kg. The Flexpicker is a delta robot, meaning that it with three arms controls a triangular plate, swivel, in a work area shaped like a cylinder. Joints using plain bearings connect the arms.The plain bearing in use today consists of a plastic ring which slides against a hard anodized joint ball. Despite the fact that the plastic contain friction-lowering additives, the bearing needs to be lubricated to prevent noise. Because the robot is used in food and drug handling environments, where the demands on hygiene are set very high, the robot is often washed. This results in the lubrication being washed away and more grease needs to be added.The purpose of this Master Thesis was to examine and document the possibilities of eliminating the use of external lubricants. To enable the use of softer plastics, calculations were done to determine the loads on the components in the plain bearing. Similar calculations had been made between 1997 and 1999 but we could show that they are no longer relevant. We have also found that they used a time, for the robot to complete a cycle, that didn?t match reality.We continued by performing experiments on combinations with a few, carefully selected FDA-approved plastics and joint balls with hard, friction lowering coatings. The temperature in the ungreased plain bearings was measured during running operations and we could determine which combination produced the lowest amount of friction. Also by listening for noise, we found that the combination of the hard anodized joint ball used today, sliding against the plastic Fluorosint 207, worked best. An endurance test was started with this combination and since no noise has been noted and the wear is low we believe that we?ve found a solution to the problem.Parallel to this we have studied the possibility of alternative solutions to the problem. One was to change the joint and use two separate rotations, which is tribologically favourable. This solution also eliminates the expensive spring unit that is keeping the parallel arms together. Tests where we have lowered the force in the spring unit have been performed with good results. A lower force results in less wear and makes it possible to change the shape of the spring unit. In the report we have suggested a new shape of the spring unit that lowers the cost of production