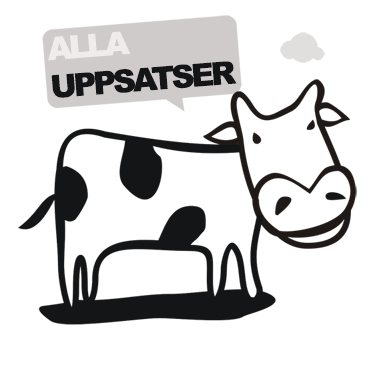
Elektrolytisk reduktion av zink vid reningsprocess
When cylinders for motor saws are manufactured there are high demands on the cylinders strength and wearing qualities. Aluminum is a material with low density and is used by Husqvarna AB for their motor saw cylinders. The aluminum is strengthening with nickel that is attached to the cylinders through electrolysis. When aluminum is in contact with oxygen a film of oxide is formed. To eliminate the oxide and to prevent formation of new oxide zinc is used. The cylinders are dipped into a bath of zinc before they pass on to a pre-nickel process, which purpose is to remove the excess of zinc so the ?real? nickel process won?t be contaminated. In the process there is a selective bath where zinc is precipitated on sheet-metals through electrolysis. The problem is that while zinc is precipitated so is nickel and in a much greater extend, about 1 % zinc and 99 % nickel.Husqvarna AB needs a technique to increase precipitation of zinc and reduce the precipitation of nickel. A small copy of the selective bath was constructed where adjustments of different parameters were possible. In the bath there was an anode of nickel, a cathode, process liquid, a pump for stirring and a plant installation from an aquarium for the temperature. In the bath different voltages, distance between anode ? cathode and different sheets of metal were tested. Every test were in progress for about three days and then pieces of sheet-metals were cut and sent for analysis of zinc/nickel percentage.A couple of the tested sheet-metals didn?t work and the ones that did work showed no special difference in zinc/nickel percentage. An increase in distance between the anode and cathode showed a small difference but not much. The alteration that showed to be most effective was to decrease the voltage. The normal voltage is 2, 8 V but when it was decreased to 2, 0 V it gave a much better result. The layer on the sheet-metal showed to contain 12 % zinc and 88 % nickel. A couple of other tests were performed with decreased voltage but no one gave as good result as 2, 0 V. If Husqvarna AB shall be able to use a lower voltage they need a greater cathode surface then they have today. That is because of the lower reaction rate. The lower reaction rate conducts an increasing amount of zinc in the bath and an electrolysis that doesn?t work completely.Other methods for precipitation could have been tested e.g. change of anode, precipitation of zinc as a salt or a powder that could have been filtrated or a process that reduces the excess of zinc. To test any of these methods big changes in the process structure would be needed which costs both time and money. The authors therefore concluded that the best thing for Husqvarna AB to do is to increase the cathode surface by connecting another bath next to the existent.