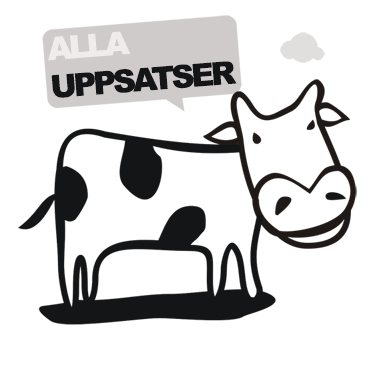
ENERGIÅTERVINNING I GRANSHOT® - PROCESSEN
Uvån Hagfors Teknologi AB (UHT) has developed a process ? GRANSHOT® ? for quicksolidification of metals in water baths. In the process liquid metal is splintered ? granulated ?into small drops. The drops are rapidly cooled in a water bath where all the heat energy from theliquid metal is transferred into the water. The granulation is often performed with great metalflows, normally 1-4 tonnes of metal is granulated per minute. The energy that is transferred fromthe liquid metal to the water is about 300 ? 400 kWh per tonne depending on type of metal andcurrent metal temperature in the granulation process. In normal applications the water is allowedto gain a temperature of 60°C before it is cooled to the surrounding temperature in coolingtowers or in heat exchangers. Because of drastically increasing energy prizes and in some caseslack of energy resources, it is very interesting to try to recover the energy the water contains.The purpose of the project is to perform a study of the energy flow in the GRANSHOT®-processand analyse different methods to make use of the developed energy. The investigation containanalyses of the economical consequences of an eventual implementation of the most suitablemethod in the GRANSHOT®-process and a simple layout design of a granulation facility withimplemented energy recovery technology.An extensive pre-study is executed to investigate different types of existing energy recoverytechnologies and what they need to operate. The possibility to modify different electricityproduction technologies to suit an implementation in the GRANSHOT®-process are alsoinvestigated.The most suitable energy recovery technology for the GRANSHOT®-process was found to be aproduct built on the Organic Rankine Cycle (ORC) called Powerbox, developed by the Swedishcompany Opcon. When analysing the effects of a Powerbox installation in a high capacitygranulation facility with a yearly tonnage of 3 million tonnes the big water flows results in aneed of 10 Powerbox-units. Despite an estimated efficiency of only around 4 % and investmentcosts as high as around 100 million SEK, the repayment time is as short as from just over 2 yearsup to around 5 years. The repayment time is depending on the electricity prizes, and thereby inwhich country the facility is situated. The project has also resulted in a basic layout modelled ina computer aided design program, displaying key components and water flow paths.