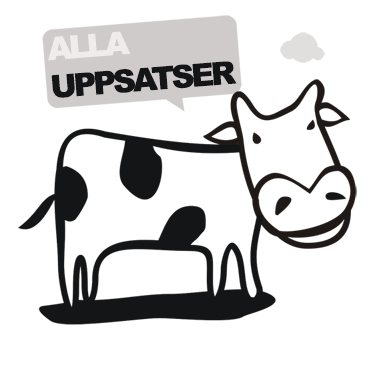
Design and evaluation of an AGV-system for Tetra Pack in Lund using simulation
This examination work is the final work in our education to become a Bachelor of Science inMechanical Engineering by the University of Lund.The main purpose with this work has been to develop a new effective material handling system for TPPM AB in Lund since the existing system starts to become out of date. The future system that is going to be installed shall have the capacity to support all machines with unit-, semi- and finished goods during full production. The work has also included studying the possibilities to change the material flow in a positive way between the storage and the production when one is using existing buildings.During our work we have been used a simulation program called AutoMod, performing company visits, interviews and reviewed internal and external information to create a picture of what the best conclusion can be. During the work we have contacted five suppliers to receive system solutions and quotatioris. The suppliers, which have been contacted, are Swisslog, Moving, Rocia, Christensen & Hansen and ABB. To be able to receive quotation concerning construction work on the buildings the company NCC, AB Lunds Rörmontering and Systemprojekt AB were contacted.Concerning the solution of AGV-system we have reach to that they can be concluded to three which all has laser system for navigation. Alternative 1 is that a new one will replace the existing system after being suited for present production. If this alterative is choosed it also means that the existing material flow and breakdown during wintertime remains. The most common problem concerning the AGV-forklift is that the security equipment is very sensitive against snow. The result of this is that the front bumpers activates and the AGV-forklift stops. Adding problems related to the laser system for navigation are strong sunlight, fog and heavy ram. The amount of AGV-forklifts for this alterative will be 11 where one of them is used to transport foil racks.Alterative 2 means more radical changes. To be able to carry out this alterative not only investments in a new material handling system is needed but also changes in existing buildings. To further increase the effectiveness of the material flow the AGV-forklifts working pattern is reversed so the direction is going clockwise instead of anti-clockwise as today. The gains by doing this is that when the AGV-forklift has delivered material at machine 3616 it can also pick up rolls at machines 3612, 3610 and 3616. The system that we are suggesting is a combination of AGV- and conveyor system. In a combination like this the AGV-forklifts are going to provide all the machines with raw- and semi material while the conveyorsystem are going to compensate today's transports of finished goods on pallets. Since you eliminate all the AGV-transports between buildings 105 and 113 in this alterative and only keep them between the buildings 107, 108 and 111, you can build the problems away concerning the weather sensitivity. The construction work that is current is to build roofs and walls like those who are being used today outside building 108. By doing this we are convinced that one is going to eliminate prior problem concerning snow, fog and sunlight. Since this alternative also bring in changes concerning activities in some of the buildings one also have to make some reconstruction in buildings 111, 113 and in some way even in 105.The largest rebuilding are going to be needed in buildings 111, 113 and contains new heat and ventilation equipment, new shipping office and a new loading dock. The amount of AGVforklifts for this alterative will be 7, where one of them is used to transport foilracks. Alternative 3 looks like alterative 1 but means that the forks on the AGV must get extended to be able to transport more than one pallet of finished goods which is the case today. In this alterative earlier mentioned problems concerning heavy ram, fog and sunlight will remain. When we have spoken with AGV-suppliers, this alternative has not been mentioned because the decrease of the AGV-forklifts was not big enough. Though we can mention that if this alternative is choose it wouldn?t involve enormous extra costs to extend the forks. Problems that can occur is a deterioration of the AGV-forklifts moving pattern since it's length is extended to 2,5 meters which is 0,7 meters more than today. Using telescope forks can of course solve this problem, which fells out during possible pallet transportation but the cost by doing this will increase prominent. The amount of AGV-forklifts for this alterative will be 10 where one of them is used to transport foilracks.By choosing alternative 1 the costs will approximately be 9 535 000-11 650 000 SEK excluding tax, where Moving has the lowest price and Swisslog the highest.By choosing alterative 2 the costs will approximately be 20 337 500-22 262 500 SEK excluding tax, where Moving has the lowest price and Swisslog the highest. It can though be of interest to notice that the materialhandling equipment in this alterative varies between 8 925 000-10 850 000 SEK excluding tax. As an extra comment to the prices in alternative 1 and 2 it can be worth mentioned that Rocla not have been able to give a price on installation outside normal workingtime. What you can assume from this is that the total price not is going to decrease but more likely increase. Other costs on 11 412 500 SEK excluding tax is bounded to the rebuildings which includes heat- and ventilation costs. These facts are the main reason why alterative 2 is so much more expensive than alternative 1. Though these differences in price are so large one still must consider the advantages that alterative 2 have compared to alternative 1.Concerning existing heat and ventilation equipment in building 111 it can be mentioned that it is both old and energy demanding which leads to increased energy costs. If a change of existing equipment is being made, TPPM AB can save approximately 70 000 SEK per year at a temperature of +15 °C. This correspond a decrease of the energy demand by approximately 200 000 kWh per year. An investment in a new equipment is going to mean that TPPM AB receive a heat and ventilation equipment which can be considered both as cost effective and environmental friendly for many years ahead.