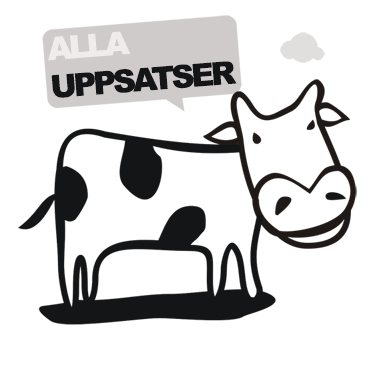
Undersökning av fosfatsbegränsningseffekter på Escherichia coli AF1000 för bättre förståelse av 3-hydroxybutyratproduktion
High quality within a Lean production system begins with standardised work, which creates stable processes able to generate predictable output. If nonconformity from the standard procedures occurs, routines are needed to analyse, correct and prevent the nonconformity from occurring again. In that way, the nonconformity can be a trigger for continuous improvements toward more stable processes. In takted production lines, where the operator follows a standard sequence with tasks set to be completed within the takt time, a nonconformity leads to downtime in the operator?s sequence, and no value is added. With short takt time, the nonconformity leads immediately to line stop and the nonconformity will be detected. With long takt time it is often possible to catch up in the sequence before the nonconformity stops the whole line. Thus, as a consequence the problem will be hidden.The aim of this study is to investigate how downtime and nonconformities can be tracked and measured in a Lean production system with long takt time, as well as investigate how this data can contribute to improvements. The study has been carried out as a case study of an assembly line at Atlas Copco Rock Drills division of Underground Rock Excavation in O?rebro. Within this case study semi-structured interviews were performed to investigate needs from data collection and improvement processes. Beside the case study at Atlas Copco, external case studies have been performed to gather information about other companies? processes. Participating companies for external case studies has been RUAG Space, AstraZeneca, Va?derstad-Verken and Saab Aerostructures.The result of the study generated three different processes, one for collecting data about nonconformities and related downtime and two parallel processes to use the data for improvements. The data collection process shows how the downtime can be tracked to support investigated needs. The downtime data is also complemented with information about key factors that affect the accuracy of the downtime measurements. The different type of downtimes that are gathered from the process is the deviations total recovery time, recovery time affecting production and downtime for the entire production line. Together with the time measurement the nonconformities is categorised and described with attributes and text to make a thoroughly analysis possible. Analysis tools proposed for the gathered data is pareto analysis, trends, calculation of cost of poor quality and identification of areas with overcapacity. Also, the result shows how some classic TPM-indicators can be used in the analysis.The gathered data can then be used in two developed improvement processes, one for reactive improvements and one for proactive improvements. The reactive process aims to in a systematic manner find corrective and preventive actions for detected nonconformities with high impact on the production. The nonconformities are handled one by one like the procedure for many deviation systems for product quality assurance. The proactive improvement process focuses on patterns in historical data about major nonconformity areas. Together with high level KPI:s and SMART goals to support high level goals, the nonconformity areas helps to identify which activities to carry out in order to fulfil the goals.