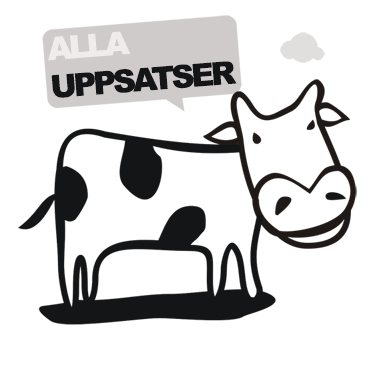
Konceptstudie av en kompakt Picker robot
Picker robots are often mounted close to each other above a conveyor belt. To be able topack robots even closer, it is desirable to reduce the footprint of the robot?s base. One way toachieve this is to skew the arms of the robot which makes it possible to move them closer toeach other.This Master Thesis has been carried out at ABB Corporate Research. The purpose is toevaluate the benefits and drawbacks for the idea of making today?s Picker robot morecompact by skewing the arms. The concept is taken from the FlexPLP-Project in which asimilar robot named Deltapod was skewed. For the Deltapod robot a smaller footprint couldbe achieved without reducing the workspace and robot stiffness too much. The evaluation ismade by investigating the changes of the following properties:?The size of the workspace?The size of the footprint?The internal forces and joint torques required for different tasks?Sensitivity against disturbance forcesThe robots are modeled and investigated by using Modelica, which is an object orientedlanguage specifically designed for modeling large systems governed by differential algebraicequations.The skewing of the arms is based on keeping a characteristic angle of the structure. Inthis way the stiffness of the robot is somewhat kept. The same approach was used for theskewing of the Deltapod. The results show that skewing the robot is probably not the bestway to achieve a smaller footprint since the workspace shrinks faster than the footprint forincreasing skews. This problem was not encountered in the FlexPLP-Project. An explanationfor this phenomenon is given in the thesis. Other negative effects due to skewing are:increasing internal forces and larger sensitivity against disturbance forces.In addition to the rule of keeping the characteristic angle, two skewed Pickers based onachieving the smallest possible footprint are also investigated. The resulting positioning ofthe arms is interesting because it cannot be made without introducing a skew to the robot.One of the robots is chosen to have a large workspace compared to the footprint, while theother is chosen to keep the relationship between the workspace and the footprint. For boththe robots the disadvantages are larger internal forces, joint torques and sensitivity againstdisturbance forces. Since the angles of the structure are not considered, the stiffness of therobot can be expected to be worse than for the Picker.